Steel construction
We have a wide range of production methods in our metal processing. In addition to the usual steel types such as S 235 and S 355, we also process high-tensile steel types such as S 400 and S 690 for special requirements in cab construction. CNC laser cutting or CNC sheet metal benders ensure the precision needed for the subsequent manual assembly process. Special, in-house developed welding equipment facilitates the process considerably.
ALUMINIUM
We have been specialising in the production of especially light cabins in aluminum materials for more than 20 years. We are one of the leading manufacturers of aluminum cabins.
Plastics / Composit
Using the widest range of plastics in combination with sheet metal enables us to build efficient cabins with the latest designs. High-tensile composite materials substitute metal, vacuum moulded elements encase and bridge, and PUR elements with high-quality, grained soft-touch surfaces can be used in the high-quality interior. Gluing devices with the appropriate process management enable cabins to be assembled with various materials and pre-fabricated components.
Production
Implementing the construction always starts with the production of the individual components. CNC laser cutting or CNC sheet metal benders ensure the precision needed for the subsequent manual assembly process. The cabins are welded together, and in part glued, using in-house welding equipment.
Coating
We use the cathodic dip coating method to make entire steel cabins especially resistant to corrosion. In our facilities, we use liquid coating for both base and top coats to provide an especially high-quality finish. In order to improve the corrosion protection even further, we offer powder coating.
Assembly
In our assembly we use state-of-the-art gluing processes. Components of various materials (such as steel, glass, GFK or ABS) are durably and reliably joined together using our equipment. The cabin customised for the end user requires especially precise process engineering. Only in this way can varied components be installed for cabins to be created according to customer specifications. We work just in sequence and deliver punctually and in the required quantity. An optimisation of the supply chain means we are able to guarantee short delivery times.
Final inspection
All cabins are checked for optical, electronic, electrical and mechanical faults in the final inspection. This guarantees proper functioning according to the documentation. We simulate all vehicle-specific functions by flashing the software and checking these for faults.
Contact us
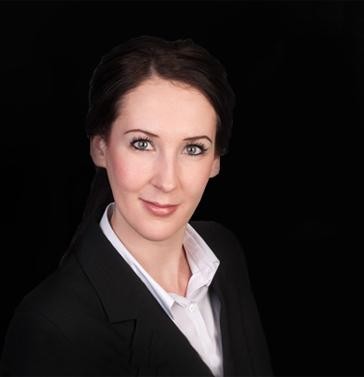
Manuela Petz
Manager Sales and Marketing
Tel. +49 15154655303
manuela.petz@mskmatec.de